Somerville Shive Analyser
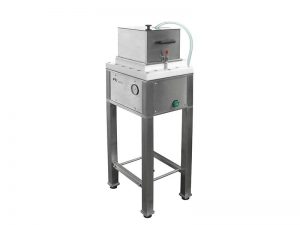
Applicable standards:
TAPPI T 275
TAPPI UM 242
PAPTAC C.11P
Product code: 40170
Features
• All parts made of non-corrosive materials
• Standard slot plate with 0.15 mm width
• Slot plate with 0.08 and 0.1 mm width optionally available
• Control cabinet for wall mounting included
• Can be installed on a PTI Bauer-McNett fibre classifier
Documentation
Description
From top down, the screening device consists of a rectangular screen box, a screen plate, a diaphragm chamber with a weir box attached and a stand. The diaphragm chamber is attached to the stand. Before each run, the screen plate is secured between the diaphragm chamber and the screen box by locking clamps. Gaskets above and below the screen plate make the assembly watertight. The screen plate is made of 316 stainless steel. There are 756 slits in the screen plate arranged in 6 columns of 126 slits each. Slit pitch within a column is 2 mm. The entire slit pattern on the screen plate measures 250 × 300 mm. The slits are 45 ± 0.5 mm long by 0.15 + 0.005 / -0.01 mm wide (the slits near the nozzle are shorter). A spray nozzle with 12 equally spaced horizontal holes is mounted at the centre of the screen plate. The holes are equal in size and are positioned 2 mm (measured from centre of hole) above the screen plate surface. The spray nozzle is calibrated for a flow of 8.6 ± 0.2 liter / minute at a water supply of 124 ± 5 kPa. A rubber diaphragm in the diaphragm chamber is connected to an eccentric mechanism which in turn is driven by a motor. The eccentric runs at 700 ± 10 rpm and creates a vertical movement of 3.2 ± 0.1 mm maximum movement for the diaphragm. At the flow rate of 8.6 liters/minute, the height of the weir in the weir box maintains the water level inside the screen box at 102 ± 2 mm above the screen plate surface.
Test description
A sample of diluted pulp is prepared – normally the equivalent of 50g oven-dry material (It is not recommended to use more than 80 or less than 20 grams of oven-dry material in a test). Assemble the device by putting the screen plate and the screen box in position, fix with the fasteners and connect the water supply to the spray nozzle. Pressing the start button starts the flow of water into the screen box. At a water level of about 25 mm the sample is added and the water pressure checked or set to 124 ± 5 kPa. When the water level reaches the top of the weir the start button is pressed again to start the timer The motor will stop at the end of 20 ± 1 min. Lifting the weir a little drains the screen box. All the debris remaining on the walls of the screen box and spray nozzle are rinsed on to the screen plate. The water hose is disconnected and the screen box un-clamped and removed. All the debris collected on the screen plate is flushed into a sample container. The suspended debris in the container is now ready for further processing (such as forming a pad for observation or quantification).
Specifications
• Standard slot plates
– 756 slots in 6 rows
– Slot-width 0.15 mm
– Slot-length 45mm
• Optionally available: slot plates with 0.08 an 0.1 mm
• Calibrated ring-jet (8.6 l/min at 123.8 kPa)
• All parts in contact with water are made of non-corrosive materials
• Vertical movement of membrane: 3.2 mm
• Motor: safety class IP 55 (690 to 700 rpm)
• Control cabinet for wall mounting
• Spraying nozzle and hose for cleaning included
• Ready for use delivery (plug & operate)
Technical data
Electricity: 230 V, 50/60 Hz
Water supply: 2 bar min (drinking water), Drain: ¾” hose
Compressed air: None
Dimensions (WxDxH): 50x45x110 cm
Net weight: 88 kg
Gross weight: 140 kg